My linear power supply arrived today, and it’s big and heavy as I expected. After poring over data sheets and doing more research and fretting and calculating, I decided to step down to a 48V supply for my stepper motor drives. Based on the torque vs speed curves and the other specs of my motors, it seems like a reasonable voltage, and should result in good torque and no overheating of the motors.
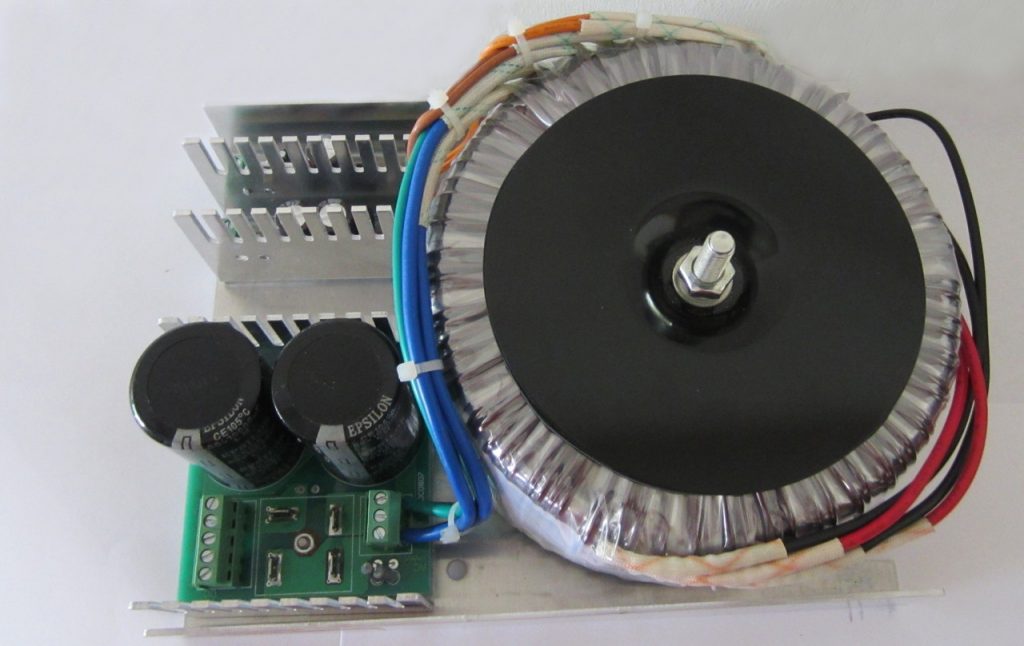
I’ve also been collecting bits and pieces here and there as I find them on ebay or other places. I’ve got a few switches which should come in handy, most especially the e-stop mushroom button. I ordered the Gecko G203V stepper drivers last week and they should arrive soon as well. Expensive as heck, but I didn’t want to screw around trying to design my own – for once I just want something that will work.
My plan is to breadboard the system electronics on a piece of plywood and use the CNC to machine the faceplate and rear panel of the final enclosure, which will likely be rack-mount.
Hopefully the CNC conversion kit will arrive some time next week, then the real work begins.. Turning a pile of metal and electronics into something useful!