Hauled the column back down to the shop and mounted it back on the machine. Sure is a lot heavier than it used to be!
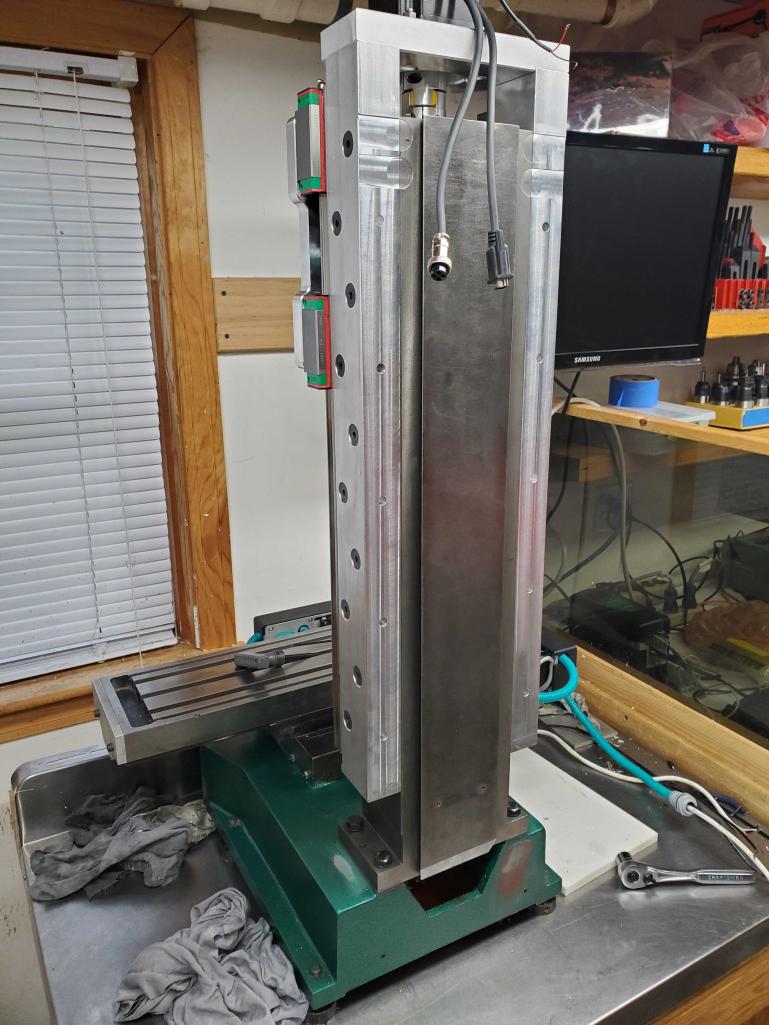
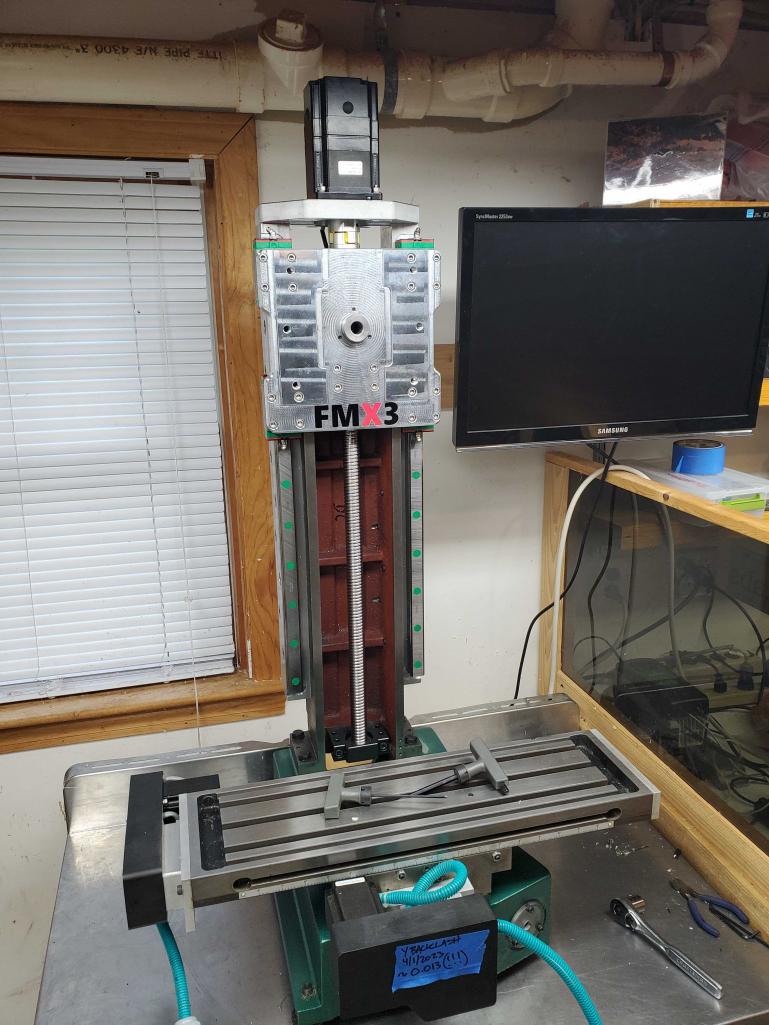
Muscling things around was a theme for today. It took some careful work to hoist the head back onto the table and get the tramming pivot aligned with the hole in the back of the head. But once aligned, it all bolted up beautifully. It’s extremely satisfying when parts mate up like they were designed.
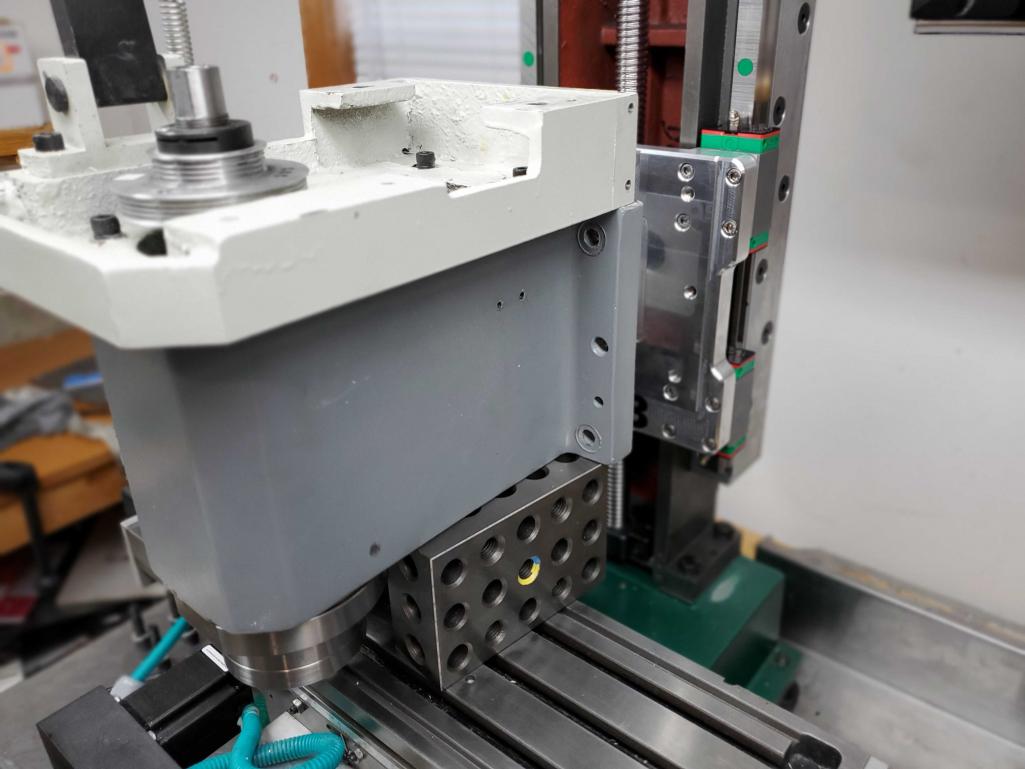
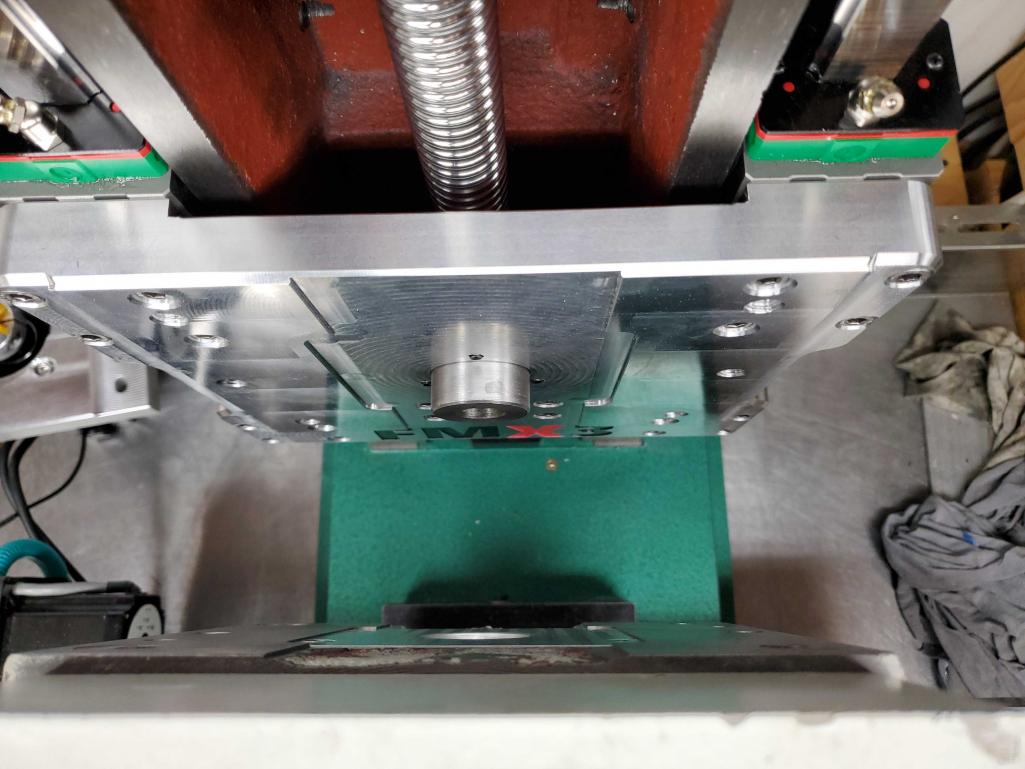
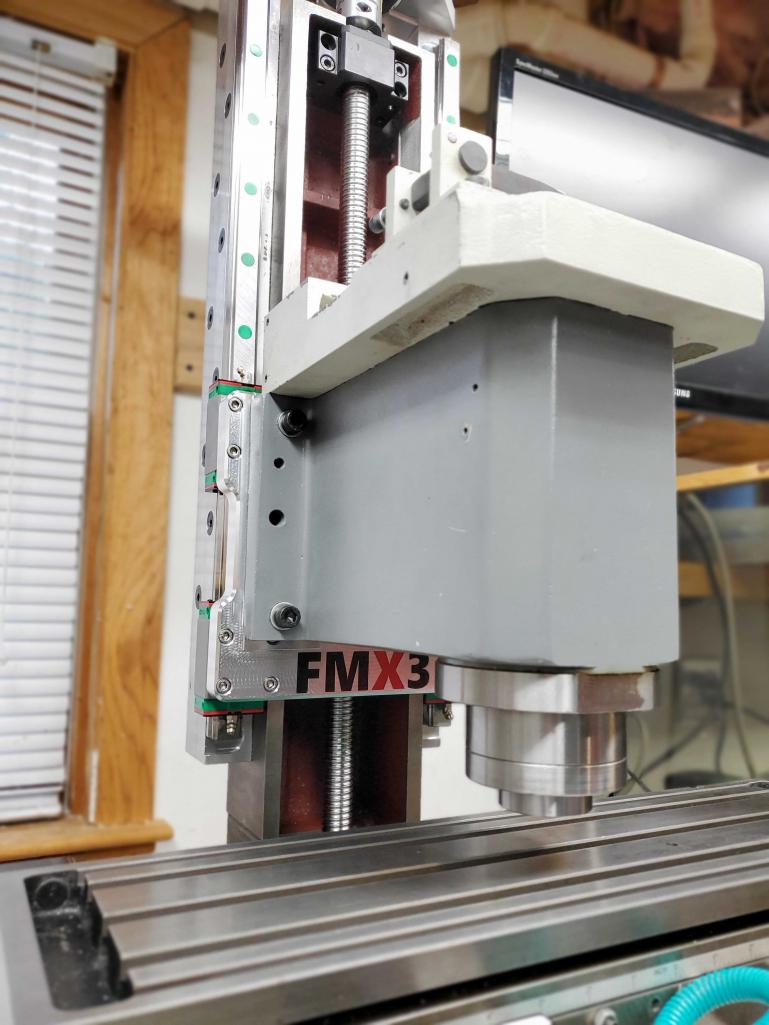
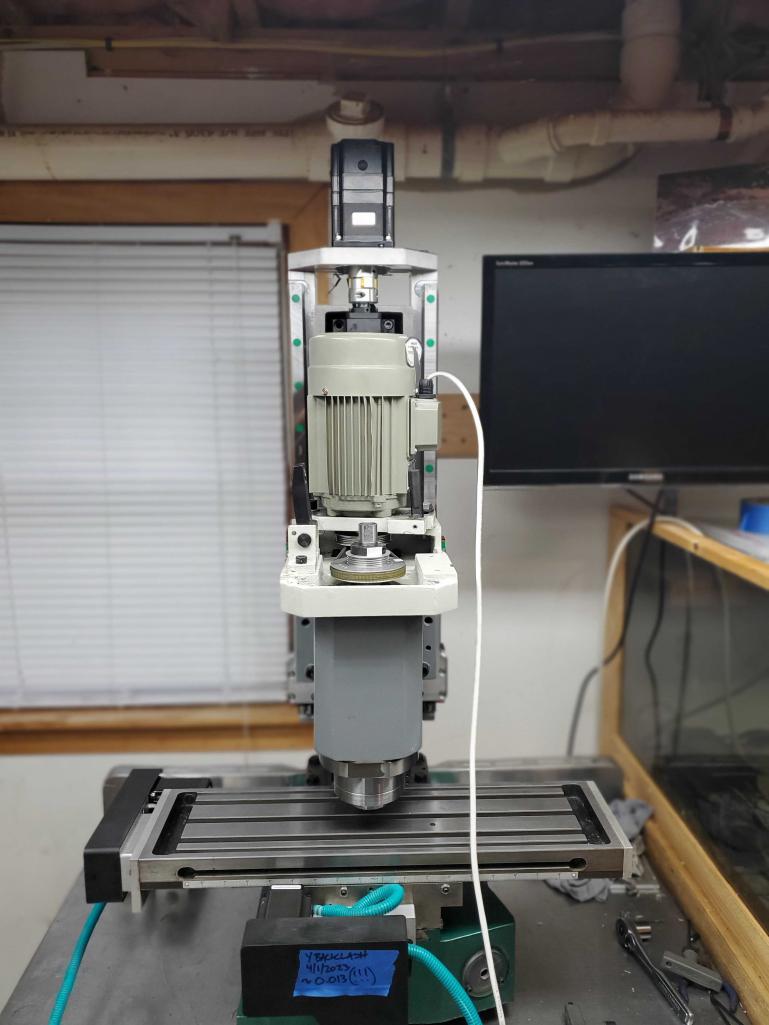
By this point it was getting late and I was tired, but I wanted to get it powered up and moving around. Here’s a shot of the chaos in progress. I’m re-doing the control electronics as part of this 10-year revisit. What you see on the bench is the partial breadboard of the new electronics clipped onto a DIN rail. The old electronics enclosure is the gray rack box on the right. And the sticker is a good reminder for a shout out to the folks at our awesome makerspace, MakeIt Labs!
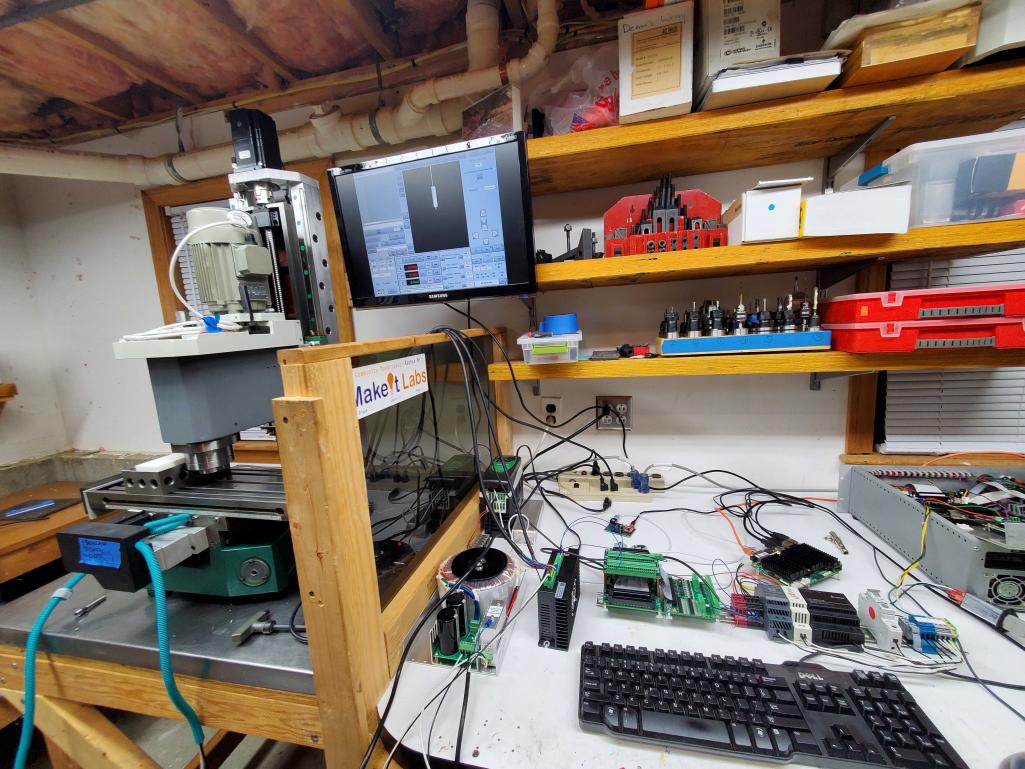
Maybe I buried the lede a bit here… but it moves under full weight with little effort, at somewhat blistering speeds (for stepper motors anyway) – 190IPM!
I was much too tired to get into checking squareness and tram last night, so that will have to wait until next time. But this is a great milestone for the last few months of effort, and the last 14 years of owning and tinkering on this machine.
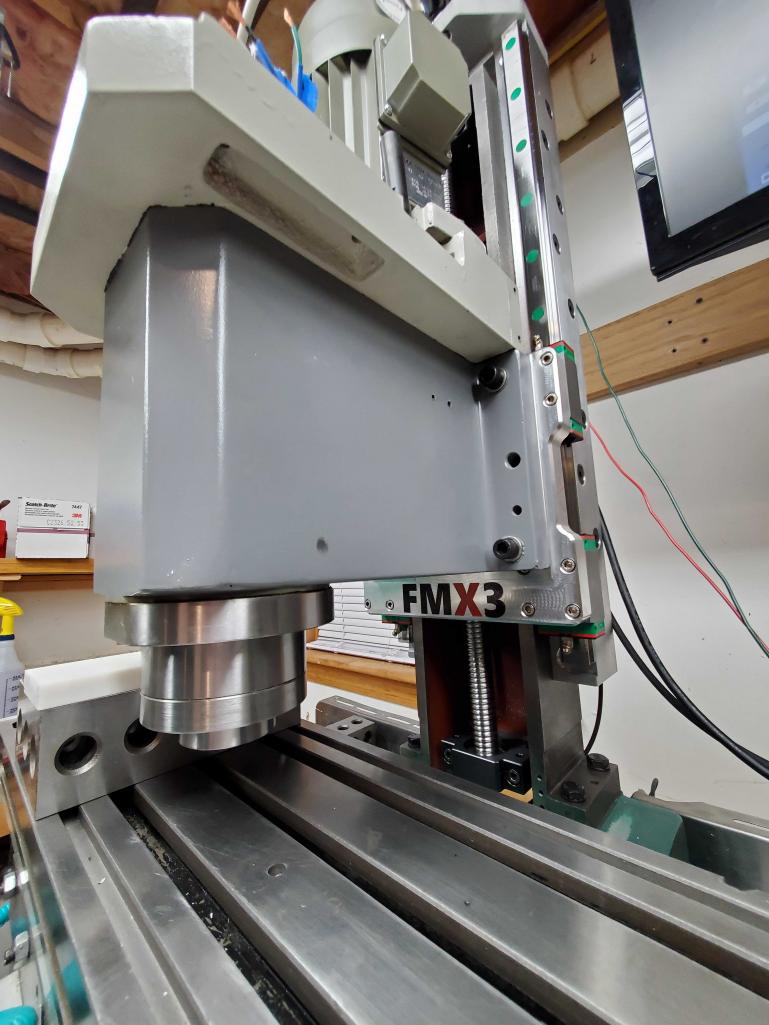