So, let’s get this thing mounted and reassembled. I re-installed the spindle, put on the belt drive sub-plate, and wired up the motor to the VFD.
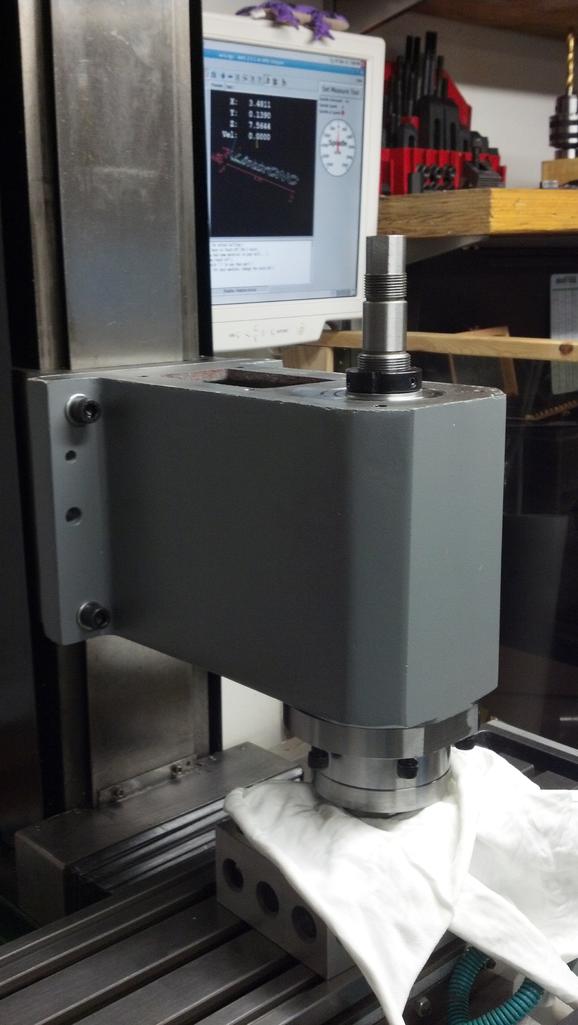
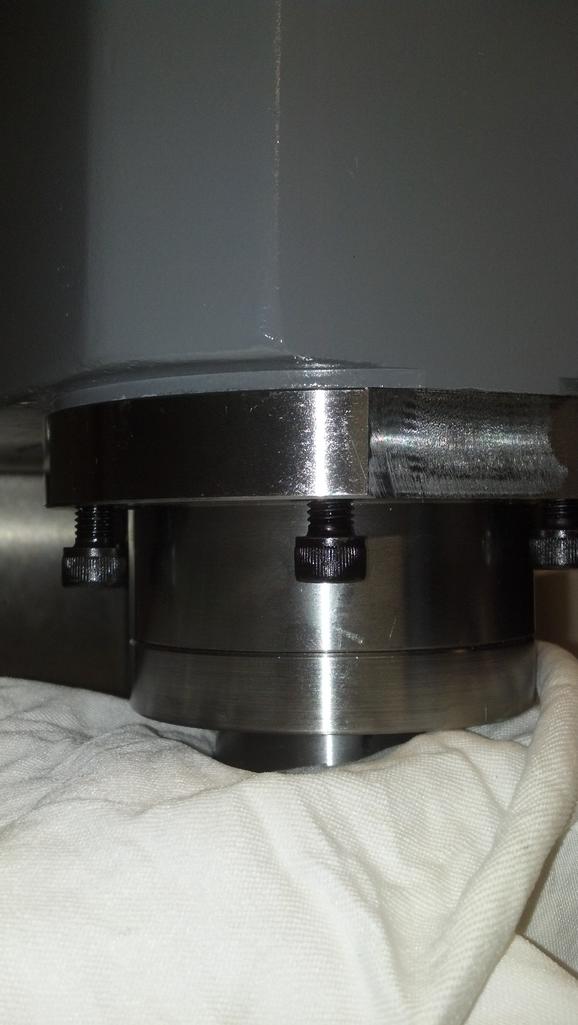

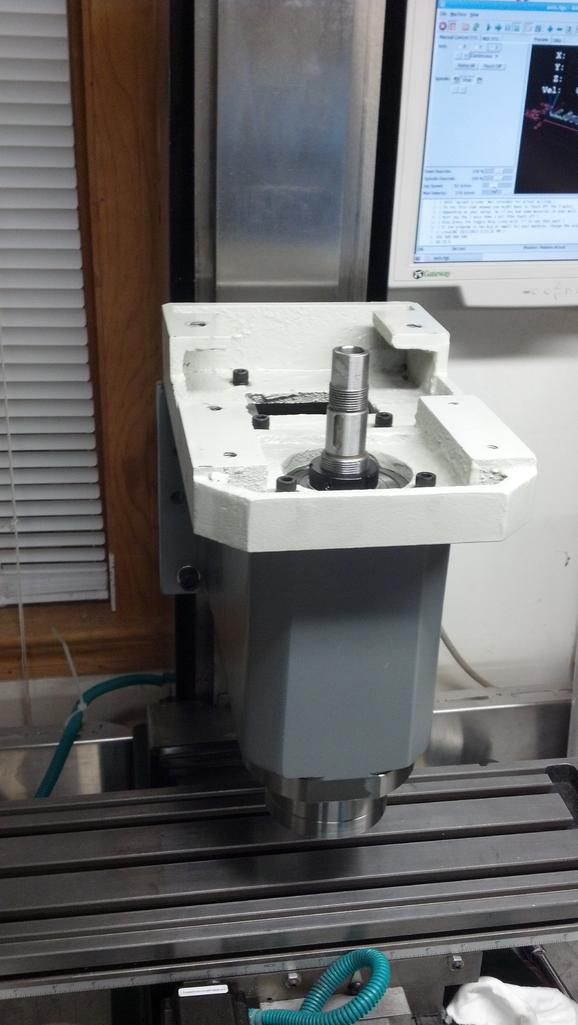
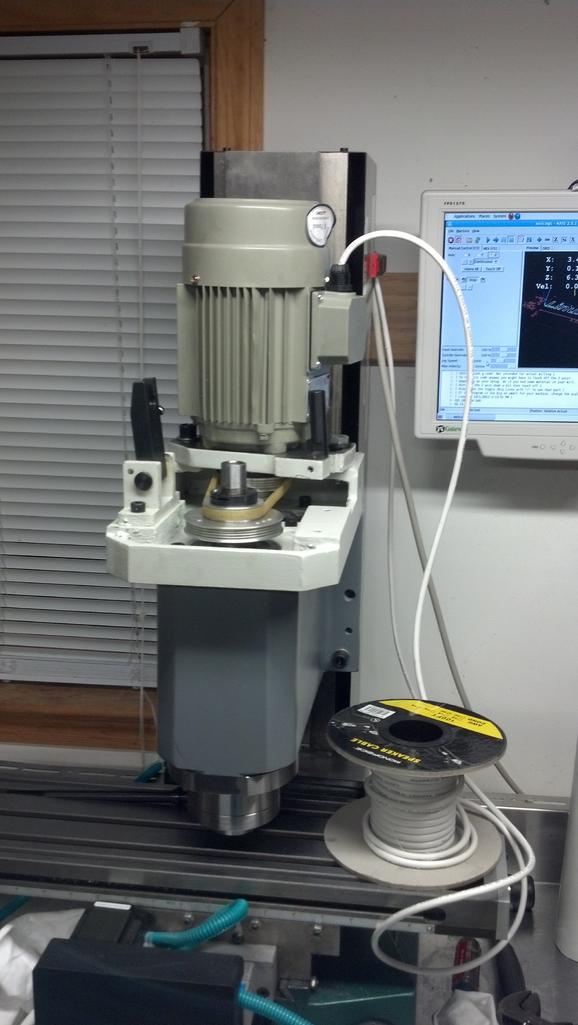
But, another serious WTF. I tried fitting an R8 collet into the spindle and it didn’t fit! Turns out the locating pin for the collet was too long. What the heck kind of quality control is this? Thankfully I got the pin down to the right length with my rotary tool and a small die grinder. Here’s a mirror shot looking up into the spindle, before I ground the pin down.
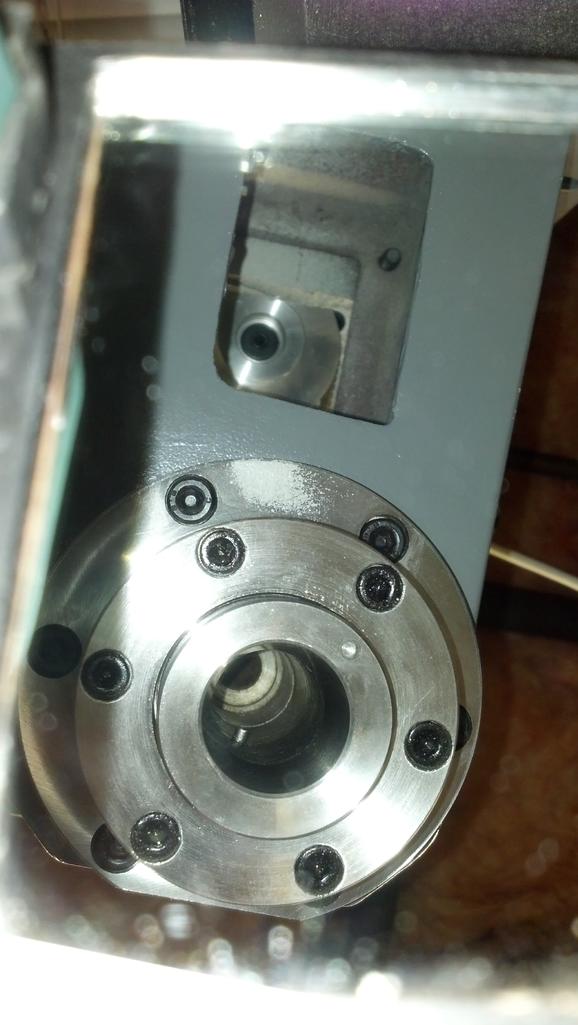
Even with the locating pin ground down to the right length, the Tormach TTS collet binds up once it’s about 3/4 of the way inserted. I eventually got it to fit, but it took pulling it in with the drawbar. Thankfully it didn’t get stuck, but it’s too tight. I tried one other regular R8 collet that I had around and it binds in the same place, but I couldn’t get it to pull in. I guess I will need to get in touch with Tormach. I can deal with cosmetic problems in stride, but this impacts actual performance and it’s unacceptable for something this expensive. This is the actual precision part for crying out loud.
But given that I could get the R8 TTS collet to fit… You know what that means. Time to make CHIPS!
Very promising results! The thing just spews chips out like crazy. And they look like proper chips! I’ve cut lots of aluminum on this machine over the last couple years, but the chips never looked like this, and I was never able to take cuts this aggressively. The cut just sounds a lot healthier too – not having that horrible gearbox in the stock X3 is really nice.
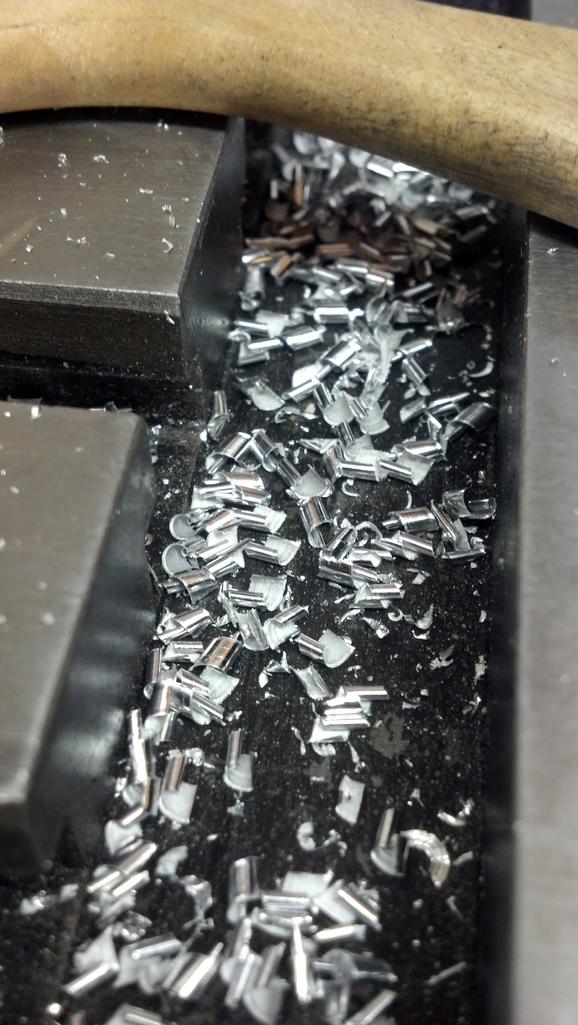
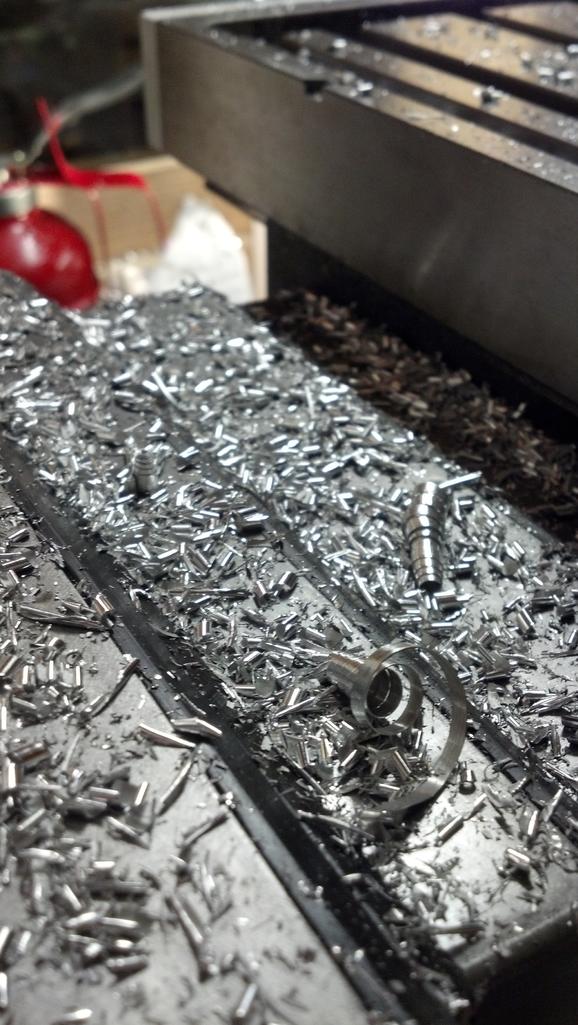
The finish was not bad given this was fairly aggressive and it’s not trammed. The scrap was partially unsupported in the vise, so the finish varies depending on the position of the cut.
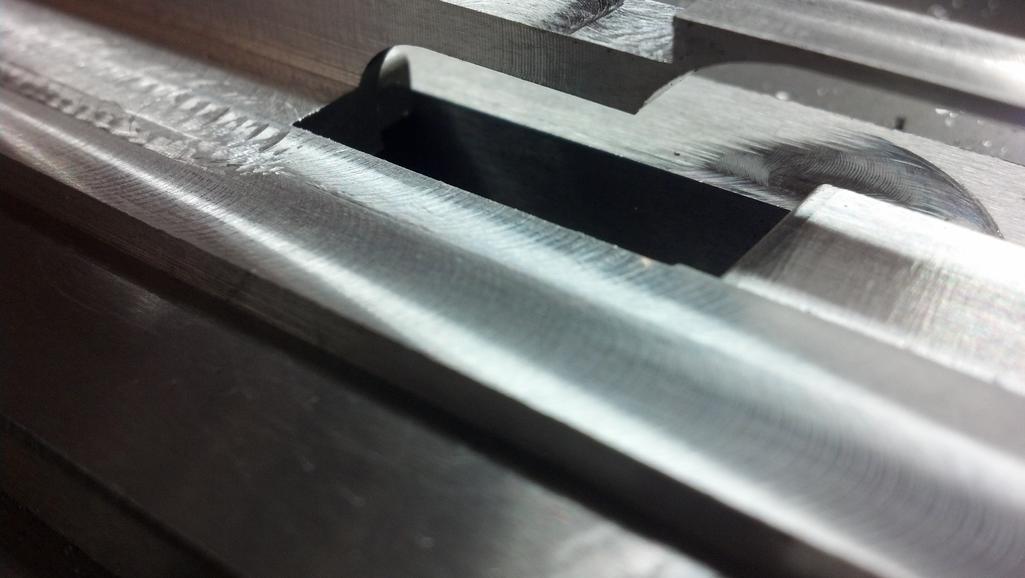
And here’s another quick test, using small end mills at high RPM.