Had some time the other evening to do the final machining on the new stepper mount, on the Tormach 1100. Being able to rough cut it on the waterjet made fixturing so much easier. Two setups, both held in the vise with the back jaw moved to the outside for extra capacity. Used our new Hallmark probe to probe the hole center for origin. Quick and easy!
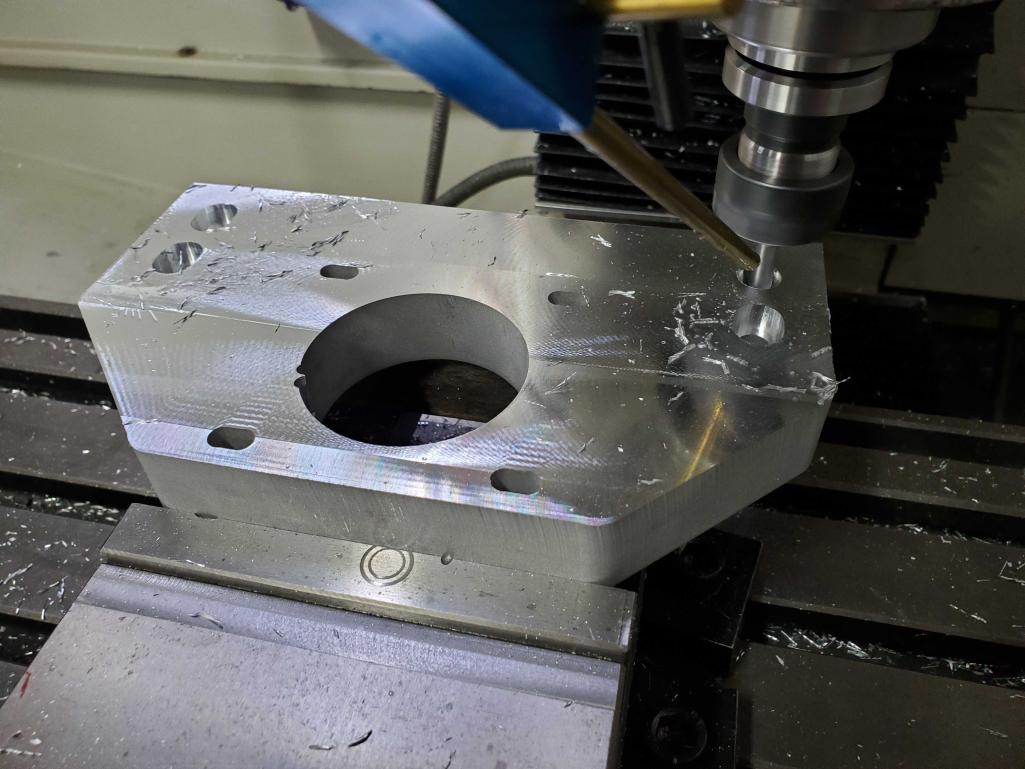
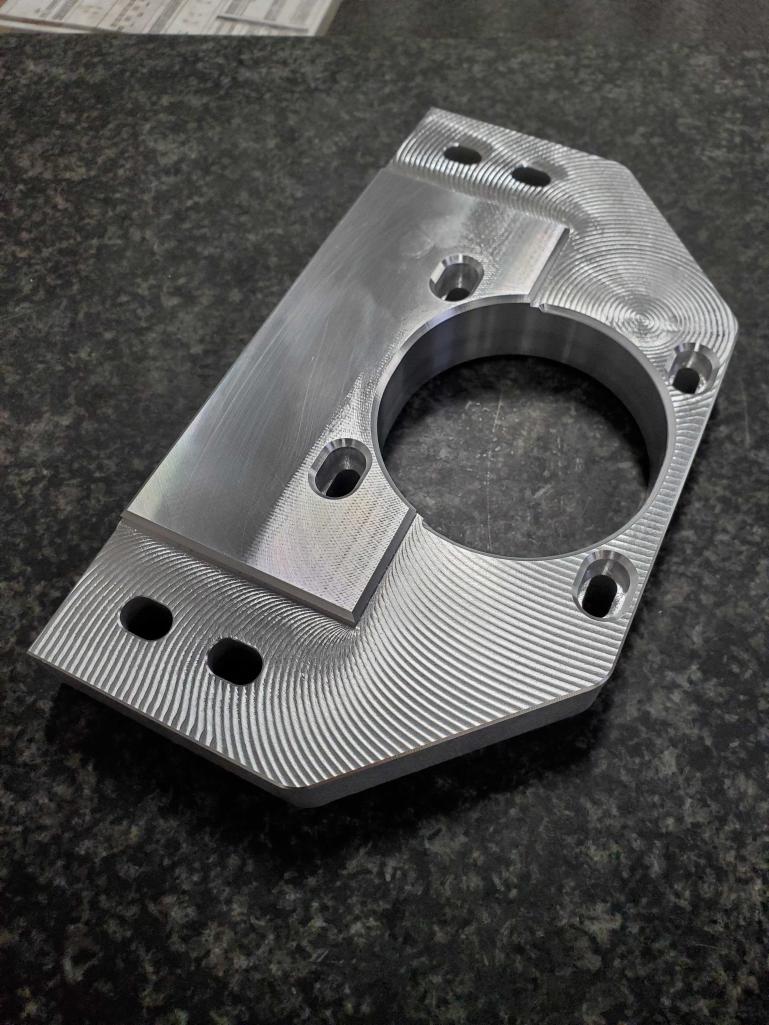
The resulting part came out pretty nice! It’s certainly shiny.
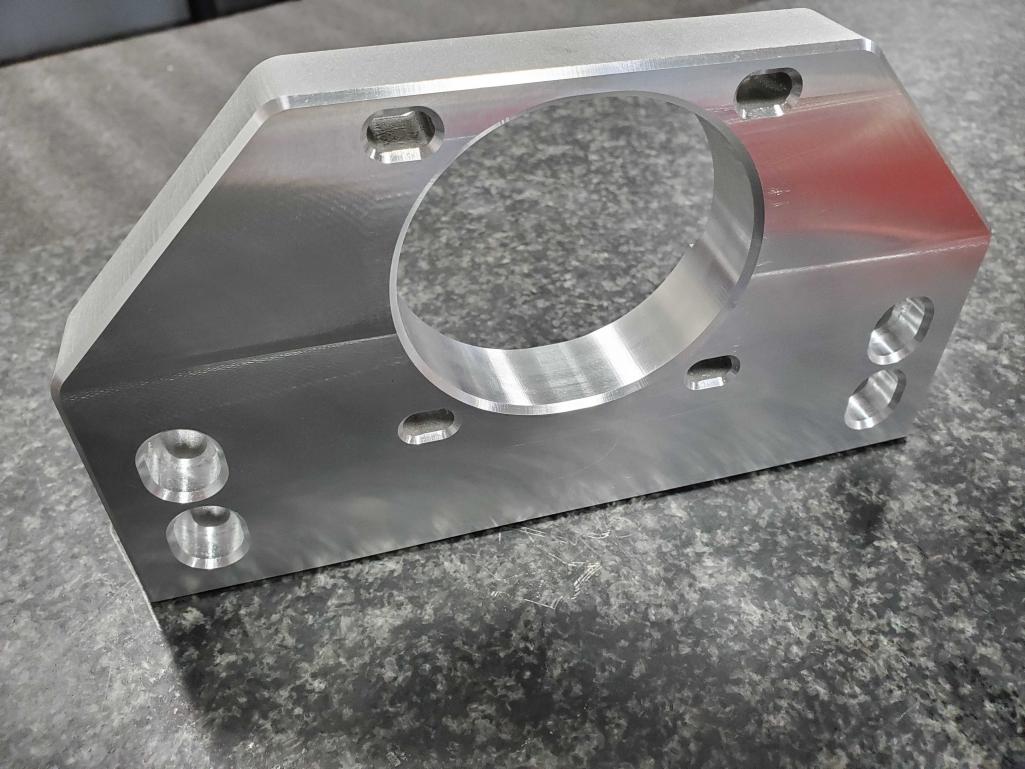
After machining, I needed to do a little bit of fitment work. Had to remove about 0.004″ (~0.1mm) on each side. Wrapped the broad side of the file in masking tape, exposing only the skinny edge – worked great!
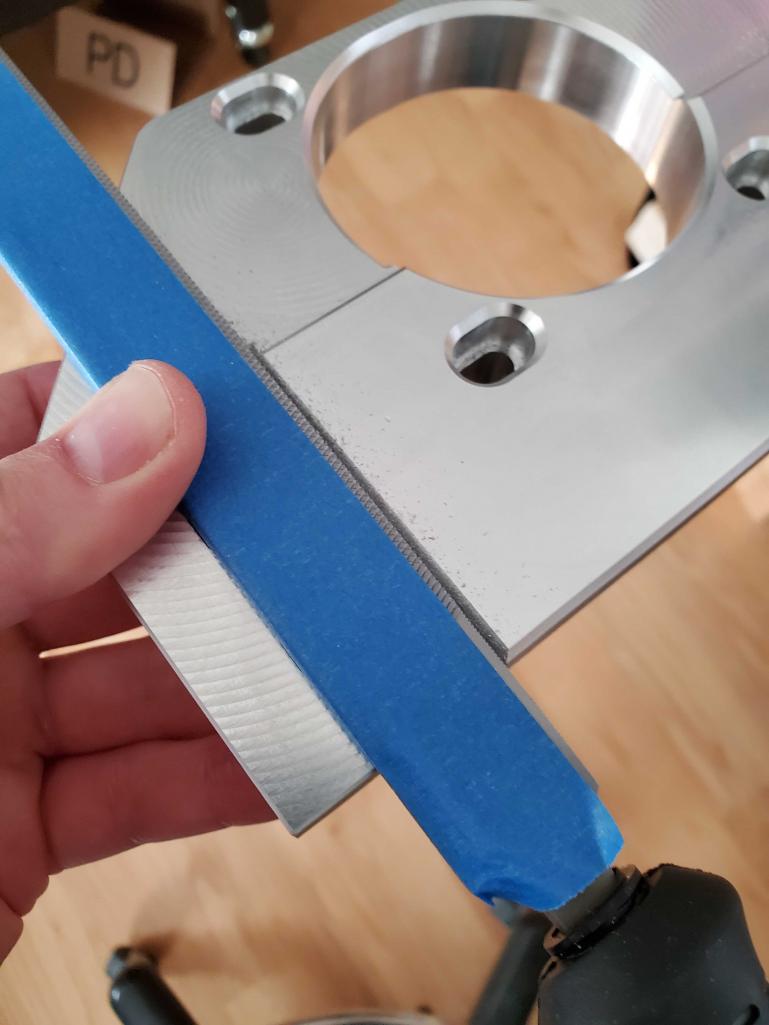
And in order to mount the new plate to the column, I had to get creative with a drill press setup. I needed to drill four holes in the tops of the new aluminum side bars. A bit wonky, but it worked, more or less.
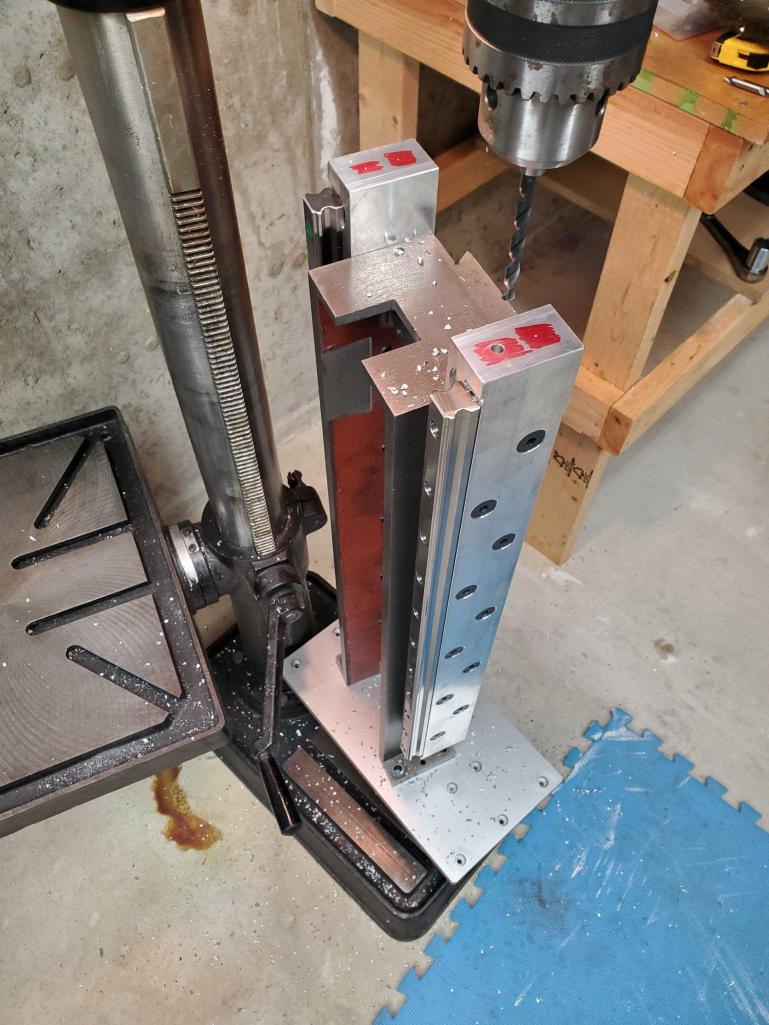
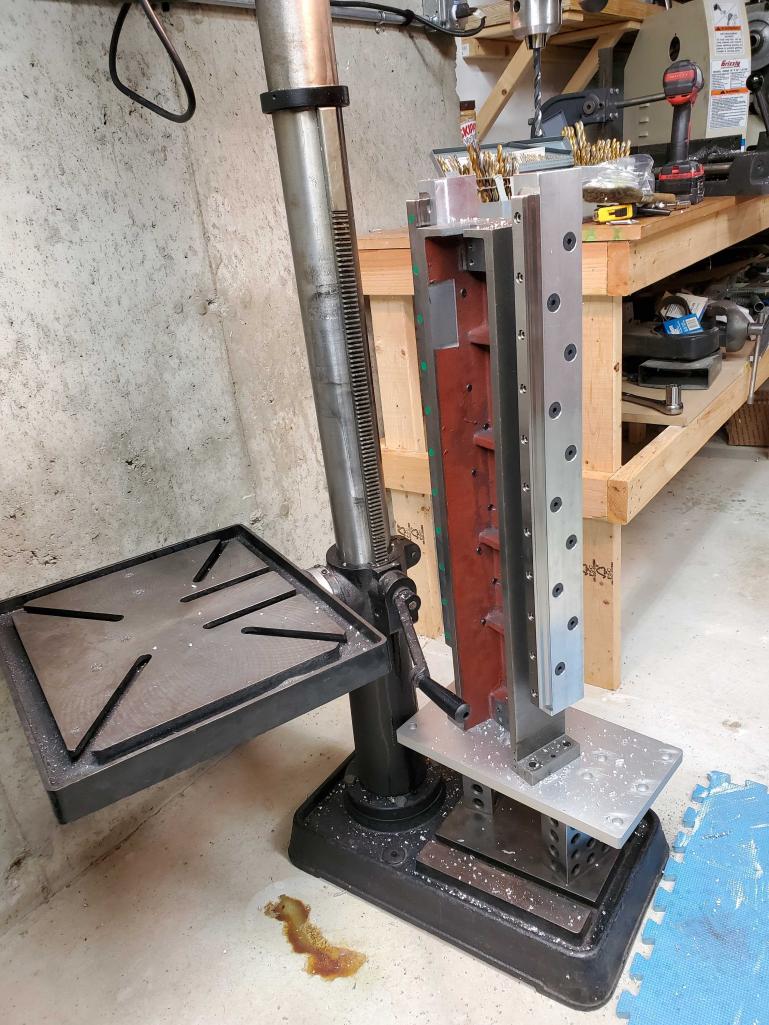
And here is the new Z stepper plate roughly bolted up and spinning the ball screw!
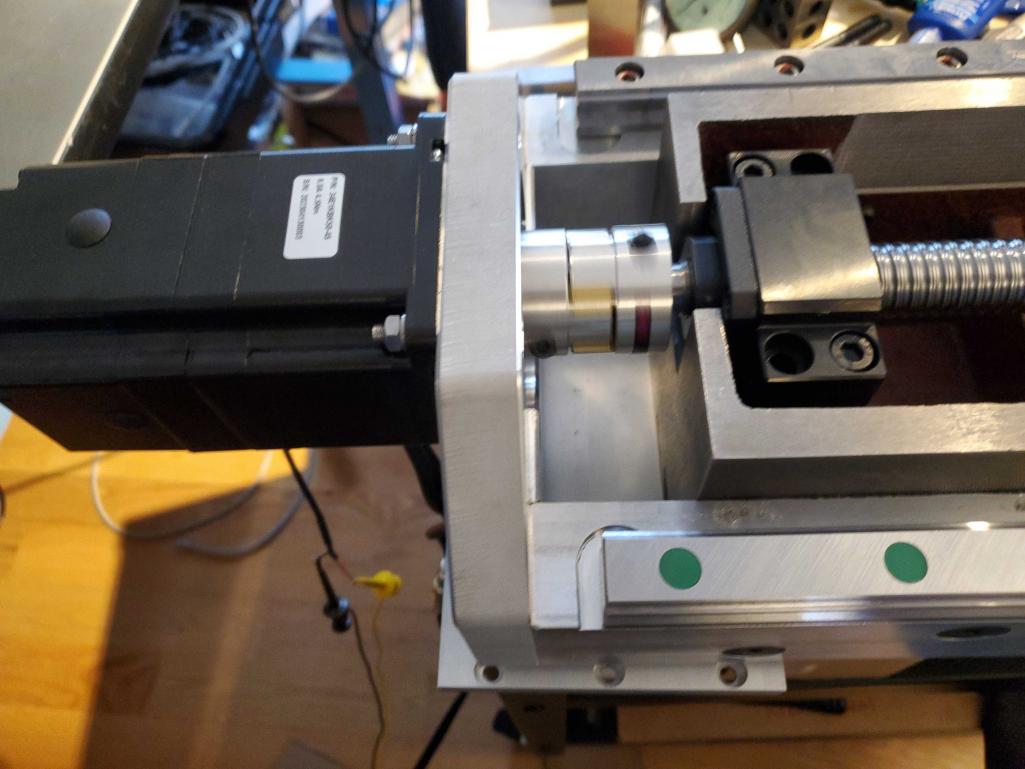